SCHOOL OF PUBLIC HEALTH
WASHINGTON, D.C.
ANGIE TEJADA
MECHANICAL OPTION
General Building Data
Bounded by K Street NW, New Hampshire Avenue NW, and 24th Street NW, just by Washington Circle and a few block away from the White House, architectural design proved to be a challenge due to the historical character of the neighborhood, strict zoning regulations and the unusual triangular geometry of the site.
The design was driven by the different space types required in the program, a desire to create an integrative space to promote interaction between faculty and students, and a strong commitment to sustainable design. The program includes classrooms, laboratories for the school’s science department, offices for faculty and administration, auditoriums, a convention center with 4 different meeting rooms, lounges for students and faculty, as well as study areas and kitchenettes. Spaces with different functions were designed around a central sky-lit atrium, which serves as the core of the building and brings daylight penetration into the narrow interior.
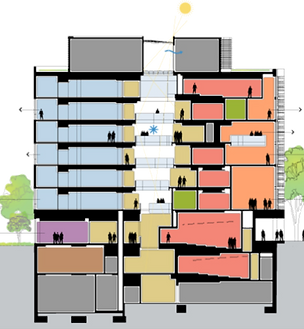
ARCHITECTURE
The building façade is composed of various materials that respond to the diversity of the urban environment that surround it. The north end, facing Washington circle, features a granite base with glass curtainwall on top, and large windows arranged within angular concaved frames along the circle. The south end faces an important intersection and has a more open glass curtainwall that extends all the way to the ground, with the intention of promoting interaction with the nearby park and streetscape. The west end façade, which faces a mostly residential area, contrasts the more public facades with the use of terracotta rain screen panels designed with a variety of horizontal patterns as the primary material, with smaller windows embedded in them to interact with the brick and masonry residential properties nearby. Finally, the east end façade uses a combination of terracotta panels and curtainwall to respond to the architecture and materials used in the building across from it.
In order to bring daylight into the narrow footprint of the building, a sky-lit central atrium space was designed running the entire height of the building. A second atrium space, also running the entire height, was added near the southern end to allow light entering through that façade to reach the entire building. This curtainwall uses an integrated solar shading screen to reduce solar heat gain.
BUILDING ENCLOSURE
SUSTAINABILITY
The building achieved LEED Platinum certification through various strategies. Some key optimization features of the project are:
-
Dedicated outside air systems (DOAS) with a heat recovery wheel technology serving offices and classrooms
-
Chilled beam systems
-
Displacement ventilation for large auditoriums
-
Demand control ventilation using CO2 and occupancy sensors for all HVAC systems
-
Heat recovery chiller to provide free heat rejection to the building reheat system
-
Reduced lighting power densities and lighting occupancy sensors
-
High performance windows
-
Shading elements for southern exposure
-
Measurement and verification of energy use with sub-metering for all utilities
-
On-site storm water retention for make-up water for the cooling towers and grey-water system for toilet core to achieve water use reduction by 50%.
-
Energy efficient lighting fixture selection to achieve optimum energy usage and maximum lighting control and output
-
Daylight control system to minimize use of electrical lighting when ambient light is available.
-
Energy efficient with effective optical controlled outdoor lighting fixtures to limit site lighting pollution and achieve outdoor lighting design
-
Large green roof to make use of space not occupied by the mechanical penthouse and achieve water efficient landscaping
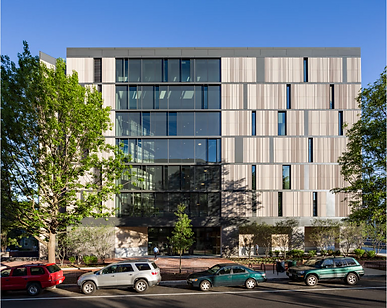
Major national codes used:
International Building Code (IBC), 2006 edition
International Fire Code (IFC), 2006 edition
International Mechanical Code (IMC), 2006 edition
NFPA 13 – Standard for the Installation of Automatic Sprinkler Systems, 2006 edition
NFPA 70 – National Electrical Code, 2005 edition
NFPA 72 – National Fire Alarm Code, 2002 edition
The site is located in R-5-E Zone District. Zoning regulations allow college and university uses in residential zone districts, provided that the campus plan has been approve. It follows the District of Columbia Comprehensive Plan, D.C. Law 16-300, 10A DCMR (Planning and Development). Zoning in the area restricted building height to a maximum of 90 ft. Since the site footprint was already small for the required program and zoning regulations required that 90% of the site be covered by new structure, the typical floor-to-floor height was reduced to 12 feet in order to insert a 7th floor.
CONSTRUCTION
The school of public health was constructed using a design-bid-build project delivery method, and involved the design building containing seven stories above grade plus two basement levels and a mechanical penthouse. The site is one of the 16 approved development sites in the university’s Foggy Bottom Campus Plan. The program includes offices, fitness centers, laboratories, classrooms, auditoriums, conference rooms, and a seven story open atrium. Construction began in March of 2012 and carried on through 2013, with occupancy occurring during the 2014 spring semester. The construction process began with interior asbestos abatement and exterior limestone removal, prior to demolition, razing, and removal of existing foundation. The shoring system (piles and lagging), bracing and underpinning were designed by a structural engineer licensed in the District of Columbia. All excavation and construction was monitored with detailed pre- and post-construction surveys of utilities and structures, which included video inspections and photographs as required by the engineer. Completion of the structure was followed by installation of piping, duct work, and conduits. After the exterior facades were completed, final inspections were performed as required before furniture installation and occupancy.
ELECTRICAL
LIGHTING
MECHANICAL
STRUCTURAL
The primary electric service at a voltage of 13.8KV is derived from PEPCO, an electrical distribution service in the District of Columbia, who also provided the distribution transformer with a 480Y/277V secondary building utilization voltage. The capacity of the primary system service was designed to serve the calculated connected load of the facility plus an additional 25% for anticipated future loads. Feeders are installed through an underground duct bank, from the secondary transformer into main mechanical space located on Basement 2 level, where they are terminated on a 480Y/277V, 3-phase, 4-wire, 3000A service entrance rated switchboard. Normal lighting distribution is provided by 400A, 480Y/277V busway. Power distribution panels contain bolt-on feeder circuit breakers, and have a capacity designed to be sufficient for the addition of 25% future connected load.
The emergency/standby power source is derived from a single 750 KW/938 kVA, 480Y/277V diesel-powered engine generator set located in a weather-proof, sound attenuated, enclosure on the roof. This emergency/standby power is distributed to three automatic transfer switches: one for life-safety loads, two for standby motor loads. Life-safety loads consist of emergency egress lighting, the fire alarm system, and telecommunication equipment. Standby motor loads include exhaust fans, stair pressurization fans, one AHU, elevators, and smoke exhaust fans. The main emergency electrical room contains emergency/standby switchboards used to distribute emergency power to loads.
A complete lighting system for all indoor and outdoor illumination was designed by Atellier Ten, a lighting consultant firm, in accordance to the standards of IESI, the Illuminating Engineering Society of North America. Total lighting energy usage was designed to exceed minimum ASHRAE 90.1 lighting energy consumption requirement. Emergency/night lighting is provided by un-switched branch circuits, fed from an emergency lighting panel. Energy efficient and advanced optical assembly type of lighting fixtures were selected to achieve optimum energy usage and maximum lighting output and comfort. In general, fluorescent and high-intensity discharge lighting is distributed at 277V, while lighting control wiring is distributed at low voltage. The ampacity of lighting circuits was sized for 25% future growth plus 125% continuous load factor, per National Electric Code standards. The majority of the fixtures have fluorescent lamps rated at 32 watt, T8, 3500K color temperature, with a color rendering index of 75 or higher. Metal halide lamps are clear and have a color rendering index of 60 or higher. Some LED lights are also used on some fixtures throughout the building.
Lighting control technology features dual technology occupancy sensors, timed-controlled lighting, and programmable low-voltage control relay system for common public spaces. Selected spaces utilize a combination of infrared/ultrasonic occupancy sensors and photocells, in order to harvest available day lighting and minimize energy consumption. All corridor lighting, except life-safety branch lighting, is controlled by a time clock. Dimmers were provided for high-occupancy spaces such as conference rooms and classrooms.
The building integrates two mechanical systems, with operation controlled by a building automation system. The first system is consists of two air-handling units, AHU-1 and AHU-2, located on basement 2 level. AHU-1 serves spaces in basement 1 and level 1, such as exercise rooms, laboratories, classrooms, a convening center, lobbies, and support areas. AHU-2 serves the auditoriums located in the basement, as well as a larger auditorium located on level 1. This system is a combination of overhead single duct variable air volume (VAV) and under floor air distribution system (UFAD), delivering supply air overhead at the perimeters of the rooms, and to the floor levels at a minimum of 64 F to maintain occupant comfort. It operates in occupied and unoccupied modes; including demand control ventilation.
The second is a Dedicated Outside Air System (DOAS) and Chilled beams. It is composed of two air-handling units located in the mechanical penthouse, which serve office and classrooms for levels 2 to 7, as well as the atrium running through these floors. The single-duct, constant air volume reheat system provides cooling, heating, and humidification to the spaces. Supply air from the DOAS units serves ceiling mounted 2-pipe active chilled beams, which provide sensible cooling for partial space cooling. Return air is centralized at the top of the atrium, and either relieved to outside via return fans or returned to the units. Each unit has two energy recovery wheels incorporated for heat recovery purpose and air treatment. Chilled water for the cooling system is supplied by three primary-flow centrifugal chillers, including one dedicated heat recovery chiller which provides heating source for reheat loads.
The primary structural system used is an exposed post-tensioned, cast-in-place concrete system. Post-tensioned slabs have more capacity to span longer distances and resist the same loads, which allow for thinner concrete sections and longer spans between supports. There is a 7” thick slab that is generally used throughout the building. Deep beams with post tensioned strands are used as girders to support the slab beams framing into it. This system was selected in order to be able to introduce a 7th floor by reducing floor-to-floor height, and to remove unique portions of each floor level for the atrium design. Typical columns supporting the floor structure consists of 24” x 24” with a concrete compressive strength of 6,000 psi.
For the structural façade design, a louver and sunscreen system is being used and supported by outriggers from the main gravity system. These outriggers and curtain wall systems are designed by the supplier, but are a unique building enclosure needing structural consideration. Minimum design loads were selected in accordance of ASCE standards, and concrete construction conforms to ACI requirements (Building Code Requirements for Reinforced Concrete).

Building Name: SCHOOL OF PUBLIC HEALTH
Location: WASHINGTON D.C.
Occupant: GEORGE WASHINGTON UNIVERSITY
Occupancy/Function Type: EDUCATIONAL
Size: 161,100 SF
Number of Stories: 7 ABOVE GRADE + 2 BASEMENT
Project Team:
-
DESIGN ARCHITECT: PAYETTE
-
ASSOCIATE ARCHITECT: AYERS-SAINT-GROSS
-
MEP/FP: AFFILIATED ENGINEERS INC
-
STRUCTURAL: TADJER-COHEN-EDELSON ASSOCIATES
-
LIGHTING DESIGN: ATELIER TEN
-
CM: WHITING-TURNER
Dates of construction: 2012-2014
Cost: $57 Million
Project Delivery Method: DESIGN-BID-BUILD